In the realm of modern 食品包装, thermoforming machines play a pivotal role, offering versatile solutions for businesses aiming to deliver efficient and attractive packaging solutions. This guide dives deep into the intricacies of thermoforming machine for food packaging, その種類を調べる, コンポーネント, 材料, プロセス, 利点, 適切なマシンを選択するための考慮事項.
What is Thermoforming?
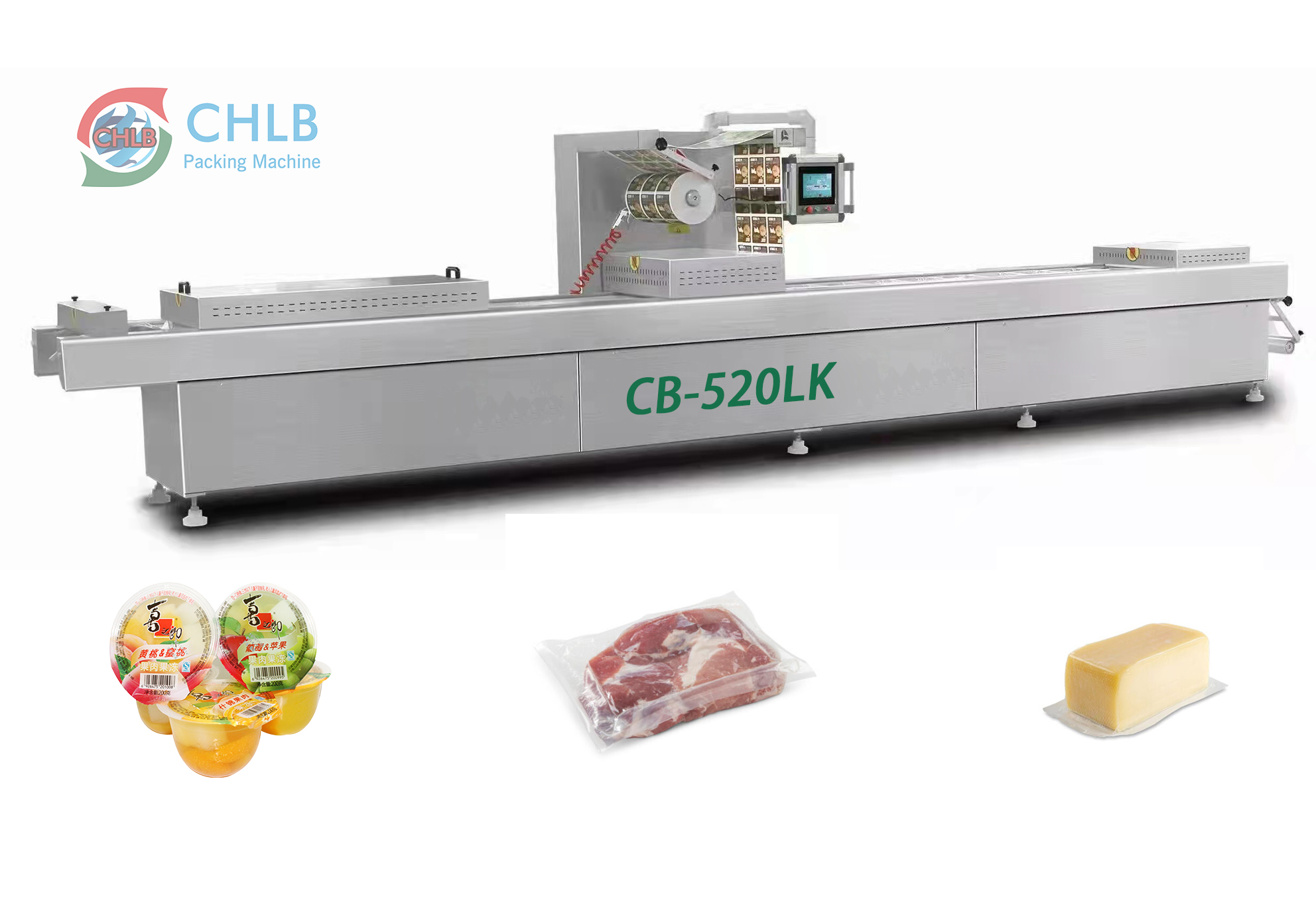
Thermoforming is a manufacturing process used extensively in packaging, where a thermoplastic sheet is heated to a pliable forming temperature, formed to a specific shape using molds, and trimmed to create the final product. This method is widely adopted due to its versatility and cost-effectiveness in producing custom packaging solutions.
Types of Thermoforming Machines
Vacuum Forming Machines
Vacuum forming involves heating a plastic sheet until it becomes pliable, then using vacuum pressure to mold it over a mold. This method is ideal for producing shallow parts like trays, ブリスターパック, and clamshells used in thermoforming packaging.
Vacuum thermoforming machines are extensively used in packaging various food products due to their ability to create custom shapes and sizes efficiently.
Pressure Forming Machines
Pressure forming utilizes both vacuum and pressure to create more detailed and durable parts than standard vacuum forming. It is suitable for complex designs and thicker materials, offering enhanced aesthetics and structural integrity. These machines are ideal for producing robust food packaging solutions that require a higher level of durability and precision.
Twin Sheet Thermoforming Machines
Twin sheet thermoforming involves heating and forming two sheets simultaneously, then sealing them together to create a double-walled part. This method is used for creating products with hollow spaces or insulated properties. It is employed in the production of containers and trays that require insulation or barrier properties, enhancing thermoformed food packaging’s capabilities.
Key Components of a Thermoforming Machine
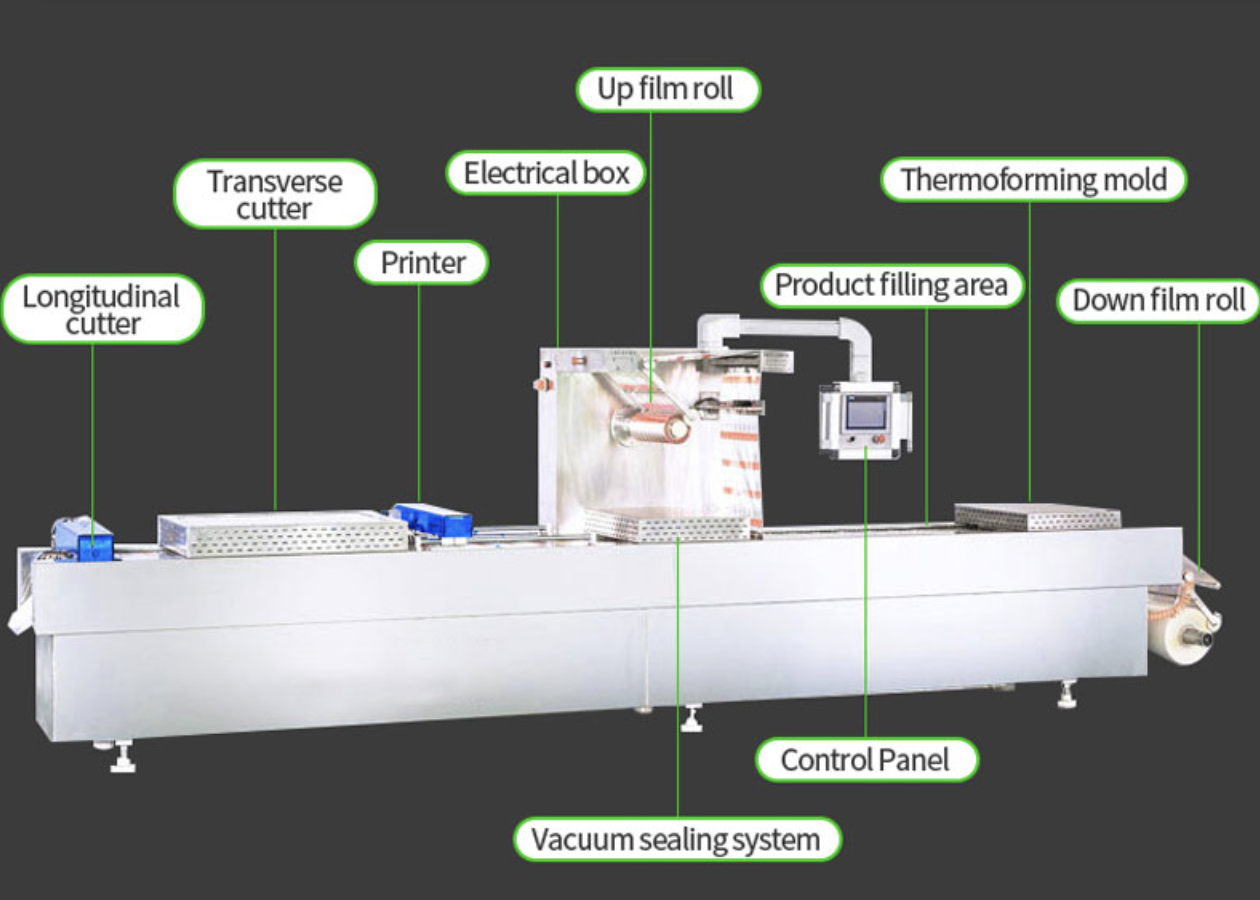
発熱体
Thermoforming machines utilize various heating elements such as ceramic, quartz, and infrared heaters to heat the plastic sheets uniformly. Precise temperature control is critical to achieving consistent forming results and ensuring the quality of thermoformed packaging.
Forming Stations
Forming stations vary in complexity and capability, allowing for customization in molding shapes and sizes based on specific packaging requirements. Modern machines offer adjustable molds and forming parameters to accommodate diverse packaging needs, from simple trays to intricate containers.
Trimming Stations
Trimming stations utilize cutting tools to remove excess material from formed parts, ensuring clean edges and precise dimensions. Accurate trimming is essential for achieving uniformity and aesthetic appeal in thermoformed food packaging, enhancing product presentation and functionality.
制御システム
Advanced control systems automate the thermoforming process, enhancing efficiency and reducing human error. Intuitive user interfaces simplify machine operation and maintenance, improving overall productivity and operator satisfaction.
Materials Used in Thermoforming for Food Packaging
ペット (ポリエチレンテレフタレート)
PET is widely used for its clarity, strength, and barrier properties, making it suitable for packaging beverages, サラダ, and bakery items.
PP (ポリプロピレン)
PP offers excellent resistance to moisture and chemicals, making it ideal for packaging yogurt cups, deli containers, and microwaveable food trays.
PS (Polystyrene)
PS is lightweight and versatile, commonly used for packaging meat trays, egg cartons, and disposable food containers.
Thermoforming Process
#1: 前処理
材料の選択: Choosing the right thermoplastic material is crucial for achieving desired properties such as clarity, 耐久性, and recyclability in thermoformed food packaging.
Sheet Extrusion: Extruding plastic sheets of uniform thickness prepares them for the thermoforming process, ensuring consistency in product quality.
#2: 形にする
加熱: Heating the thermoplastic sheets to their optimal forming temperature softens them, making them pliable for molding.
Molding: Applying vacuum or pressure molds the heated sheets into the desired shape, conforming to the mold’s contours for precise packaging dimensions.
#3: Trimming and Finishing
Cutting Techniques: Trimming excess material from formed parts using cutting tools or dies ensures clean edges and uniformity in thermoformed food packaging.
品質管理: Implementing rigorous inspection and testing procedures guarantees that finished products meet quality standards, ensuring customer satisfaction and compliance with regulatory requirements.
Advantages of Thermoforming Machines in Food Packaging
Thermoforming surpasses traditional methods like injection molding and blow molding in terms of flexibility, 費用対効果, and speed, making it a preferred choice for food packaging applications.
- 費用対効果: Thermoforming offers lower tooling costs and faster production cycles compared to other molding methods, making it economical for small to large-scale production runs.
- 設計の柔軟性: The ability to create custom shapes, サイズ, and textures allows for innovative packaging designs that enhance product visibility and consumer appeal.
- スピードと効率: Thermoforming machines can produce high volumes of packaging quickly, meeting tight production schedules and market demands effectively.
- 強化された製品保護: Thermoformed packaging provides excellent barrier properties against moisture, 酸素, および汚染物質, prolonging shelf life and ensuring product freshness.
適切な熱成形機を選択します
ニーズの評価
Evaluate your production requirements, material preferences, and desired output volumes to select a thermoforming machine that aligns with your business goals.
注目すべき主な機能
Consider factors such as heating capabilities, forming station configurations, trimming options, and automation features when choosing a 熱成形包装機.
予算に関する考慮事項
Balance initial investment costs with long-term operational savings and production efficiency to maximize ROI in thermoformed food packaging.
メーカーの評判とサポート
選ぶ a reputable thermoforming machine manufacturer and supplier known for reliability, technical support, and responsive customer service to ensure smooth operations and machine longevity.
結論
Thermoforming machines are indispensable tools in the food packaging industry, offering unmatched versatility, 効率, そして費用対効果. By understanding the types, コンポーネント, 材料, 複雑なプロセス, and advantages of thermoforming, businesses can make informed decisions to enhance their packaging capabilities and meet evolving consumer demands for thermoformed food packaging solutions.
FAQs on Thermoforming Machine for Food Packaging
1. What types of food products are commonly packaged using thermoforming?
Thermoforming is widely used for packaging products such as meats, cheeses, bakery items, 新鮮な農産物, and ready-to-eat meals due to its ability to provide protective and attractive packaging solutions.
2. How does thermoforming contribute to sustainable packaging practices?
Thermoforming allows for the use of recyclable materials and optimized material usage, reducing environmental impact compared to traditional packaging methods.
3. What are the key considerations when choosing between vacuum forming and pressure forming machines?
Vacuum forming is suitable for shallow parts and lower volume productions, while pressure forming offers enhanced detail and durability for complex designs and thicker materials in thermoformed food packaging.
4. How can automation in thermoforming machines improve production efficiency?
Automation reduces manual labor, minimizes errors, and increases throughput, enabling faster production cycles and consistent quality in thermoformed food packaging.
5. What role does material selection play in thermoforming for food packaging?
Choosing the right thermoplastic material ensures that packaging meets food safety standards, offers appropriate barrier properties, and enhances product shelf life and presentation.